Reciclagem de Plásticos
A reciclagem de termoplásticos exige certo conhecimento do pessoal envolvido com relação à matéria-prima e aos cuidados necessários para sua preparação. Quanto mais especializada em determinada família polimérica (poliolefinas, estirênicos, amidas, e etc.) for a mão-de-obra responsável pela triagem de borras, peças ou galhos na empresa recicladora ou de venda de sucata plástica, menor a possibilidade de se encontrar problemas relacionados a contaminação durante o uso do reciclado em um processo de
injeção, por exemplo.
Identificação e separação do resíduo
Muitas vezes, os resíduos chegam até o reciclador numa mistura de diversos tipos de plásticos, fazendo com que o granulado produzido fique muito rígido se essa
contaminação não for eliminada antes da
extrusão (ex.: contaminação do
ABS por
PS), ou que o espaguete estoure com frequência nesse processo (ex.: contaminação da
PA por
POM). No caso da contaminação do ABS por PS, é possível utilizar borracha butílica para reduzir a dureza proporcionada pelo PS, consequentemente aumentando a flexibilidade do produto final.
Borra (à esquerda) e galhos de injeção (à direita)
são pós-industriais
O processo se inicia com a separação da matéria-prima, que pode ser oriunda da indústria, como: peças com defeito, galhos e borras de injeção (material pós-industrial); ou oriunda do lixo doméstico, como: eletrodomésticos, telefones, peças de carro, carenagens de moto e etc (material pós-consumo). A reciclagem do pós-industrial geralmente produz um material de qualidade superior ao do pós-consumo, já que este último pode ter entrado em contato com produtos químicos como óleo, graxa, sabão ou outros produtos de limpeza durante sua utilização como produto final, fazendo com que se percam algumas de suas propriedades. Entretanto, deve-se observar o que foi produzido com o pós-industrial, pois peças de reposição de 2ª linha podem ser produzidas com material já reciclado, ou seja, a qualidade desse resíduo mesmo oriundo da indústria pode ser praticamente igual ou até inferior ao pós-consumo em alguns casos.
Outro detalhe que deve ser observado no pós-industrial é a forma em que se encontra o resíduo. No caso de borra, deve ser verificado se não há contaminações com outros materiais, já que muitas vezes o transformador utiliza o próprio material a ser injetado para “purgar” o cilindro da injetora, principalmente quando se injeta uma pequena diversidade de produtos e matérias-primas. E no caso de peças com defeito deve-se verificar o motivo deste, pois o problema pode estar no próprio material.
Sacaria, filmes e embalagens em geral.
Exemplo de materiais pós-consumo
A
identificação do resíduo pode ser realizada com o uso da chama fornecida por uma vela, onde o resíduo entra em contato e, através do odor exalado, brilho da chama, fuligem ou bolhas produzidas, o separador consegue identificar o material. Outras formas de identificação são o corte, onde se verifica a textura de sua superfície; e o som produzido através de um impacto na peça. A identificação é fundamental na definição da qualidade do produto final e o seu bom desempenho depende da experiência do separador e de sua atenção para a retirada de contaminantes.
Em alguns casos, como na identificação do ABS, é constante a confusão por parte de separadores inexperientes em estirênicos com o PS, que produz chama e fuligem parecidas, mas que possui um odor adocicado e sem o odor de borracha característico do ABS. Usando as outras formas de identificação, o corte de um pedaço da peça de ABS com um alicate mostrará uma superfície irregular, enquanto que o PS apresenta uma superfície lisa. No caso de um impacto em uma peça de ABS, o som produzido será mais grave que o da peça de PS, já que este último é mais rígido. Porém, essas formas de identificação são mais difundidas entre separadores especializados em estirênicos, da mesma forma que separadores especialistas em poliamidas têm suas técnicas para realizar a separação entre PA 6 e PA 6.6 levando em consideração a dureza e a pequena diferença de odor entre as duas, por exemplo.
Moagem
Moinho
A moagem consiste basicamente na transformação do resíduo em flocos com aproximadamente 10mm² de área através de
moinhos motorizados construídos para essa finalidade. Esse processo é fundamental para a produção do granulado e, caso não seja utilizada uma tela adequada durante a moagem (a tela é uma lamina com diversos furos que fica logo abaixo das facas rotativas do moinho), os flocos podem ficar muito grandes e comprometer o processo de extrusão, pois pode ocorrer de o material enroscar e não descer no funil da extrusora.
Nessa etapa, é importante que o responsável atente para a limpeza do moinho no ato da troca de material a ser moído, para que não haja mistura de cor e de materiais diferentes que permanecem no interior do equipamento.
No caso da moagem de resíduos de diferentes
cores, o processo segue daquele de tonalidade mais clara para o de tonalidade mais escura, pois durante a extrusão as cores escuras prevalecem e não haverá problema, por exemplo, se um material preto foi “contaminado” durante a moagem por cerca de 30% de material cinza.
Flocos produzidos a partir de peças moídas
Descontaminação
Equipamentos geradores de estática (cabines amarelas)
Essa etapa é incluída no processo em casos onde o resíduo recebido pelo reciclador está certamente contaminado e na condição de moído, granulado ou em peças tão pequenas as quais sua separação por métodos já descritos seriam impossíveis por questões de tempo e custo.
A técnica mais utilizada para descontaminação é a
separação por densidade, onde são preparadas soluções com variadas densidades utilizando-se água, álcool etílico e cloreto de sódio (sal de cozinha), nas quais alguns polímeros flutuam enquanto outros afundam na solução do tanque, sendo então separados e submetidos a um novo banho para outra separação, e assim sucessivamente, até a separação completa por tipo de resina.
Existe outra técnica para descontaminação que é bem menos empregada, onde se utiliza um equipamento gerador de estática. O equipamento é alimentado com o material contaminado através de uma rosca transportadora, o material se deposita em uma esteira vibratória que gera atrito entre os flocos ou grânulos e depois é lançado sobre três roscas. Dependendo da estática do polímero, ele é lançado a uma determinada distância, podendo cair sobre a primeira, a segunda ou terceira rosca e sendo transportado para fora do equipamento. Através da separação por estática é possível obter um índice de 95% de descontaminação para ABS com PS.
O uso dessa técnica se restringe a empresas que possuem um amplo espaço físico, pessoal especializado para a operação desse equipamento e baixa variedade de contaminação em um mesmo lote. Além disso, é utilizada em empresas que buscam certificação de sistema de qualidade ambiental como a ISO 14000, já que a separação por densidade em solução necessita de tratamento da água utilizada antes do descarte.
Códigos e símbolos para identificação de plásticos
Antes de qualquer análise química ou física do polímero para a sua identificação, as diversas resinas podem ser reconhecidas através de um código utilizado em todo o mundo. O mesmo foi criado com o intuito de possibilitar a identificação imediata de uma resina reciclável, quando já conformada por processo anterior. Consistindo em sinais de representação, este código traz um número convencionado para cada polímero reciclável e/ou o nome do polímero utilizado, ou de preponderância, no caso de uma mistura de polímeros. No Brasil, o código de identificação foi alocado pela ABNT - Associação Brasileira de Normas Técnicas, na norma NBR-13230 - Simbologias Indicadas na Reciclabilidade e Identificação de Plásticos.
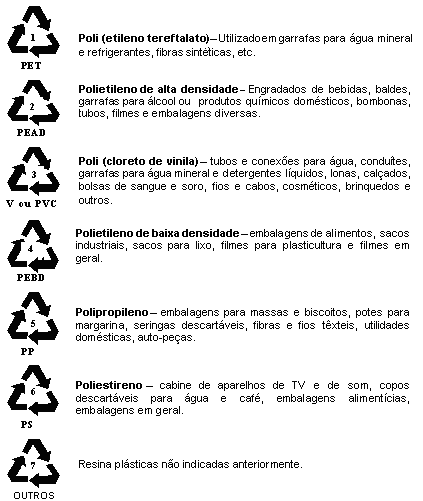
Porém, na grande maioria das vezes, estes símbolos não são encontrados nas peças produzidas em plásticos. Além disso, mesmo quando esses símbolos e códigos estão presentes, não são passíveis de confiança pois o transformador pode trocar de matéria-prima utilizada para o seu produto sem fazer alterações no
molde.
Extrusão
Silo homogeneizador
Após a separação, moagem e descontaminação, o material segue para a etapa de extrusão onde será transformado em grânulos, facilitando o processo de injeção na empresa que o transformará em peças.
Como o reciclador costuma receber lotes pequenos de matéria-prima, além das perdas durante todo o processo de reciclagem, ele pode optar pela homogeneização de vários lotes para a obtenção de um único. Isso pode ser feito através de silos homogeneizadores ou misturadores horizontais.
O material segue então para o
aglutinador, que é um equipamento construído com "facas" que trabalham em alta rotação e que possibilitam a complementação da secagem do material, além de aglomerar o material leve, reduzindo o seu volume. Aumenta a "densidade aparente", melhorando e/ou possibilitando o fluxo do material no funil alimentador da extrusora e, consequentemente, na alimentação da rosca. A aglutinação e secagem ocorrem pelo atrito das "facas" no material e por atrito entre os materiais.
Aglutinador
Depois de seco, o material pode seguir para o funil da extrusora, passando pelo cilindro dentro do qual existe uma rosca que transporta, homogeniza e cisalha o material, que se funde devido ao calor provido pelas resistências elétricas localizadas externamente ao cilindro e ao atrito promovido pela ação da rosca durante o cisalhamento. Antes da matriz da extrusora (peça que define a forma geométrica do que será produzido, no caso da reciclagem são produzidos “espaguetes”), são colocadas telas de aço que seguram as impurezas existentes no material e que poderiam provocar a quebra dos espaguetes ou entupir o
bico da injetora da empresa que faria a transformação desse plástico em peças.
Extrusora
Numa extrusora convencional, os espaguetes são resfriados em uma banheira apropriada com uma constante circulação de água, para que esta não se aqueça demais com a passagem dos espaguetes, sendo resfriada em uma torre de resfriamento.
Após passar pela banheira, os espaguetes entram em um equipamento granulador, de onde o granulado produzido segue para a embalagem. É importante que os espaguetes cheguem ao granulador a uma temperatura baixa (no máximo a 60°C), pois acima disso haverá aglomeração dos grânulos.
Veja mais detalhes sobre cada equipamento e processo
aqui.
Bibliografia:
HARPER, Charles A.; PETRIE, Edward M. Plastics Materials and Process: A Concise Encyclopedia. Hoboken: John Wiley & Sons, Inc., 2003.
CANEVAROLO JR., Sebastião V. Ciência dos Polímeros: Um texto básico para tecnólogos e engenheiros. 2.ed. São Paulo: Artliber Editora, 2002.
WIEBECK, Hélio; HARADA, Júlio. Plásticos de Engenharia: Tecnologia e Aplicações. São Paulo: Artliber Editora, 2005.
© 2010-2025 - Tudo sobre Plásticos.
Todos os direitos reservados.
Página inicial
-
Política de privacidade
-
Contato